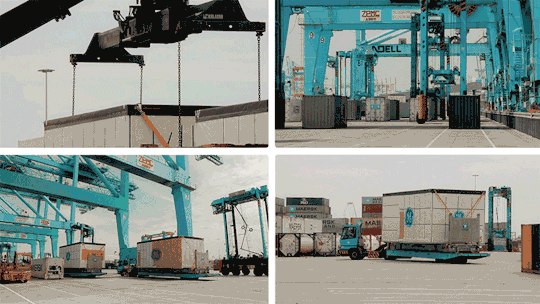
Ordering stuff online and having it shipped to your house is now as common as breathing air. But the Taiwanese manufacturer of biologics, JHL Biotech, recently upped the ante and ordered an entire high-tech pharmaceuticals factory. Made by GE in Germany, Sweden and the U.S., the components for the world’s largest single-use modular plant for making biopharmaceuticals, which the company calls KUBio, recently left Europe for JHL’s new site in Wuhan, the capital of China’s Hubei Province.
When the sixty-two completed modules that make up the factory reach the destination at Wuhan’s Biolake Science Park , they will help JHL make affordable biologics for markets where they are otherwise prohibitively expensive.
Biologics, also called biopharmaceuticals, are a new class of medicines made from strings of complex proteins. They are now leading the charge against disease and represent the fastest growing class of drugs. They range from synthetic insulin to medicines that can be used to treat cancer, rheumatoid arthritis and other diseases.
“Our vision is to make world-class biopharmaceuticals affordable and accessible to all patients,” says Racho Jordanov, JHL’s chief executive. “This revolutionary modular facility is part of the realization of our vision in Asia, where US-made biopharmaceuticals are out of reach, and there is a large unmet medical need.”
Manufacturing drugs in single-use disposable plastic containers eliminates the need for costly cleaning and sterilization. It means that facilities can be smaller, and more efficient. They can be also configured to switch quickly between different drugs.
GE Healthcare’s KUBIo includes everything from bioprocessing equipment to the building and overall project coordination. The modules at the site arrive 80 to 90 percent pre-equipped with the heating, ventilating, and air conditioning (HVAC) system, the clean room, most of the utility equipment, and all of the piping necessary to run the plant.
“It’s really very innovative and different, because today 98 percent of biopharma factories are still stick-built, meaning you design and construct the building first, then it takes around a year to get it up and running,” says Olivier Loeillot, general manager at GE Healthcare Life Sciences Asia. “Our concept is totally different because you do everything in parallel, which enables you to save up to one and half years in total [in design and construction]. This is really what is critical for companies developing biopharmaceuticals: speed.”
Once in China, GE will manage the plant’s assembly, validate the equipment and train JHL staff. The completed KUBio facility in Wuhan will have a floor space of approximately 2,400 square meters (nearly half the size of a football field) and will contain a number of 2,000-liter single-use bioreactors.
“Quality has to be built into the process,” JHL’s Jordanov says. “To control a complex process of biopharmaceutical manufacturing requires very sophisticated equipment, and very sophisticated buildings to put the equipment in.”