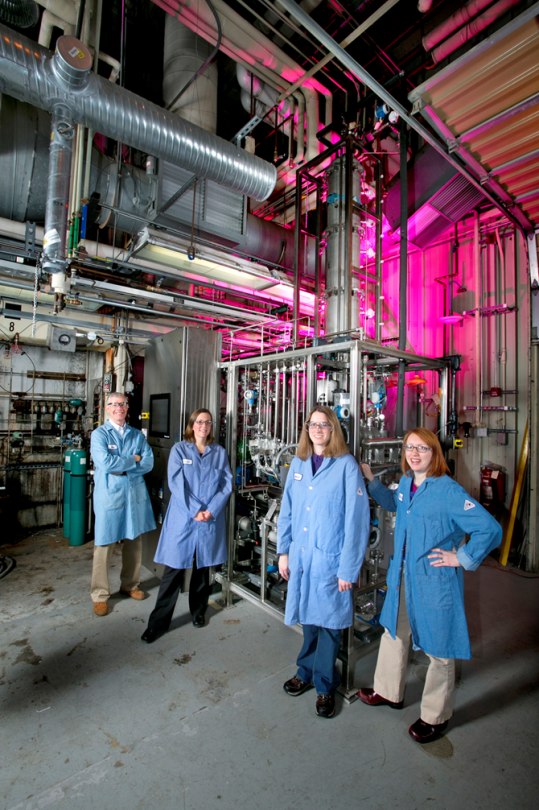
One way to reduce greenhouse gas emissions and slow down climate change is to cease burning fossil fuels. Sounds easy, but such a sudden stop would likely plunge most of today’s world into darkness and send some of the biggest and fastest growing economies off a cliff. The reality is that coal-fired power plants, the biggest emitters of CO2, are not going away anytime soon, not in the U.S. and especially not in countries like China and India which already burn half of the world’s coal and are leading builders of new plants.
That’s why scientists around the world are looking at the next best thing and developing new kinds of traps to stop carbon from escaping through the smokestack. GE’s Phil DiPietro and Bob Perry have been experimenting with a family of promising materials called amino silicones, commonly found in bathrooms and laundry rooms in hair conditioners and textile softeners. “Although they are in the same family, I wouldn’t recommend washing your hair or your laundry with the amino silicones we’ve developed,” laughs Perry, a chemist at GE Global Research in Niskayuna, NY, who spent the last decade developing the technology. “They’re specially formulated to scrub carbon.”
So far, the materials have been up to scratch. The U.S. DOE is holding a competition for developers of CO2 capture technologies. The prize: a chance to test your concept at a scale equivalent to a 10-megawatt coal-fired power plant. GE has passed the first phase and is now in the mix with five other developers to compete in the second leg.
Top: Positive results allowed Perry and his team, including from the left technologists Sarah Genovese, Rachel Farnum, Tiffany Westendorf, to scale his research from a test bench (in the background) to power plants simulators. Above: GE is testing its industrial amino silicone CO2 scrubber in Alabama. Images credit: GE Global Research
The DOE will pick two finalists from that round, who will get a chance to prove their technology at the world’s largest industrial-scale CO2 capture test facility in Mongstad, Norway. The $1 billion site will allow the teams to simulate the output of a 10-megawatt coal-fired power plant and use amino silicone to capture CO2 coming through the smokestack. “This is the big test,” says DiPietro, technical manager for CO2 capture and separation at the Oil and Gas Technology Center in Oklahoma City. He says that the Norway test would require 80 tons of amino silicone solvent and capture as much as 1,600 pounds of C02 per hour.
That would be big step for Perry and the team, who started a solving the problem of CO2 capture a decade ago with just beakers in his chemistry lab. “We’ve started moving pretty fast,” he says.
GE’s Bob Perry. Image credit: GE Global Research
Perry says that amino silicones work like a conveyor belt. They efficiently glom on to CO2 gas at about 105 degrees Fahrenheit (40.5 Celsius) and release CO2 after the mixture is heated to 250 F (121 C). The system then cools down the material and it returns to trap more gas.
Unlike conventional carbon capture methods, Perry’s process doesn’t need any water. “This is where the money is,” he says. “If you need to boil water to drive off the CO2, you are facing an enormous energy drain. The existing technology will increase your cost of electricity by 80 percent. You almost have to build a plant that’s twice as large to power the scrubber and still send some electricity to the consumer.” Perry and his team have filed several patents for their method.
The “big test” will take place at the $1 billion Mongstad facility. It will require 80 tons of amino silicones. Image credit: GE Global Research
They also designed an amino silicone molecule that’s large and heavy and doesn’t escape from the smokestack. “Our solvent is really big with high molecular weight,” he says. “Its size keeps it in the process.
The U.S. Department of Energy is running these tests because it wants the future cost of CO2 capture to be no higher than 35 percent of what it costs now. Perry says that “anyone who can get under 50 percent might be doing really well.”
Besides coal-fired power plants, Perry and DiPietro are already looking at “near-term” applications at cement plants, steel mills, small power plants and other CO2 emitters.
What about the gas? Perry says that it can be used for oil and natural gas extraction. DiPietro says that injecting CO2 down an old oil well could “yield 15 to 25 percent of the oil” originally pumped out. The gas could also help farmers grow plants. In the Netherlands, for example, farmers are using a CO2-enriched atmosphere to enhance the growth of vegetables and tulips. Now, that’s a green technology.