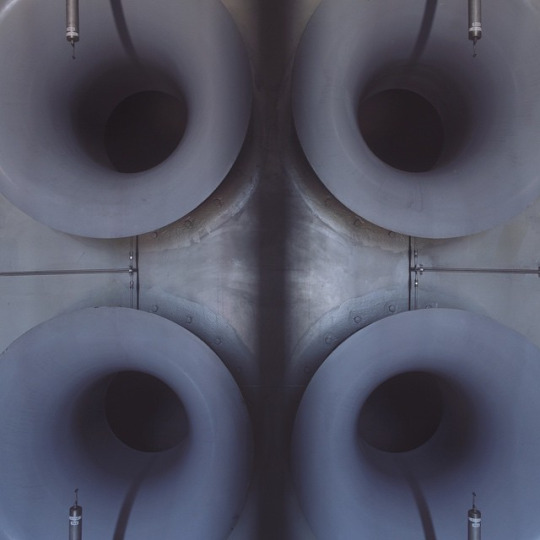
When Christine Furstoss joined GE 26 years ago, she was a hands-on materials scientist who made new turbine parts. She remembers it as a painstaking, arduous and often frustrating process.
“Two decades ago, if I had to change a material in a power generation turbine, it could take years,” she says from GE Global Research (GRC) in Niskayuna, NY, where serves as global technology director responsible for developing a new manufacturing concept GE calls the Brilliant Factory. “We would sit down and start by looking at paper drawings, ask questions, pull out our handbook of materials and figure out what was best after lots of discussions.” (You can read a Q&A with Furstoss about the Brilliant Factory here.)
But the handbooks and drawings of old have now given way to a vision of the future in the Brilliant Factory Lab at the GRC. In a darkened room, engineers can gather to look through 3D glasses to gauge how close a digitally rendered production of a design is to its original specifications. Nearby a robot inspects an aircraft blade for any imperfections with great precision.
The lab is a prototype of the new $73-million Brilliant Factory that is coming to life in Greenville, S.C., where GE makes huge gas turbines for power plants. That facility will use new production processes like additive manufacturing and advanced materials like Ceramic Matrix Composites (CMCs).
The Greenville factory, which is set to open in November, could save $100 million over three years, compared with traditional facilities, by decreasing design expenses and savings on sourcing and manufacturing. “The speed of change that I see, to me, defines this as a revolution — it is not just one change but a culture change,” Furstoss says.
It’s not only GE who will benefit from the idea. The company announced this week at the Minds+Machines conference that it would give customers access to its Brilliant Factory software to build their own version of the Brilliant Factory. Built around Predix, GE’s digital platform for the Industrial Internet, the software will allow customers like Procter & Gamble to make things more efficiently, from design and production to service in a closed loop. It could also help them to reduce unplanned downtime by as much as 20 percent.

GE is developing the Brilliant Factory inside a dedicated lab at GE Global Research. The results have already found applications inside dozens of GE plants.
Elements if the concept already at work in Pune, India, where GE opened its first “flexible” multi-modal plant last year. Workers at the plant, which covers an area equivalent of 38 football fields, will make parts for jet engines, locomotives, wind turbines, water treatment units and also the oil and gas and agriculture industries all under one roof. “The plant will allow us to quickly adjust production as demand comes in, using the same people and space,” said Banmali Agrawala, president of CEO of GE South Asia.
today announced the next version of its Brilliant Manufacturing Suite at its fourth annual Minds + Machines conference. Field-tested and optimized within GE’s own factories, the suite maximizes manufacturing production performance through advanced real-time analytics to enable all manufacturers to realize GE’s Brilliant Factory vision.
The shift to the Brilliant Factory is being driven by advances on three key fronts — data, connectivity and materials. Engineers and designers can use sensors to harvest huge amounts of data on factory floors, securely pool it in the cloud and analyze it by powerful software. New materials and rapid prototyping tools like 3D printing have also shortened the time needed to build prototypes of new parts and machines. “We can get parts through factories faster with higher confidence because we are always learning and these improvements lead to us being more cost effective, which boosts the bottom line,” Furstoss says.
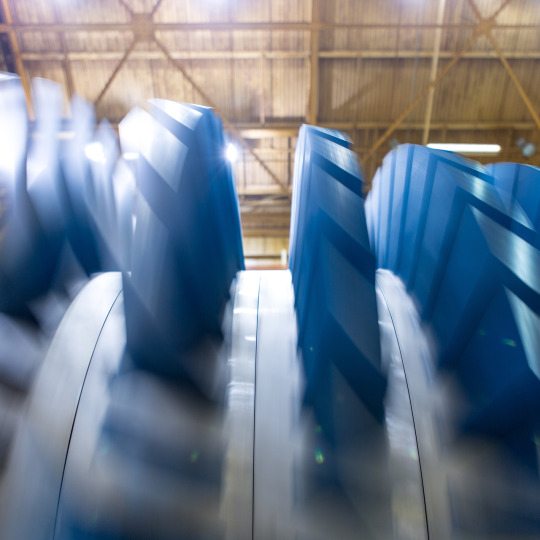
At Minds+Machines this week, GE opened the Brilliant Factory to other companies, including Procter & Gamble.
For example, using 3D printing, tool production that once took six months now takes three weeks, and “agile,” computer-guided welding can increase productivity four fold. Globally, every single percentage point increase in factory productivity could save GE an estimated $500 million per year.
Furstoss says the Brilliant Factory is also possible because of the GE Store– the sharing of ideas and expertise between GE’s various businesses. For example, ultrasound technology from GE Healthcare is now used in factories to inspect blades for wind turbines. “We can inspect parts as they are being made, using the same ultrasound technology we use in our medical machines,” she says.
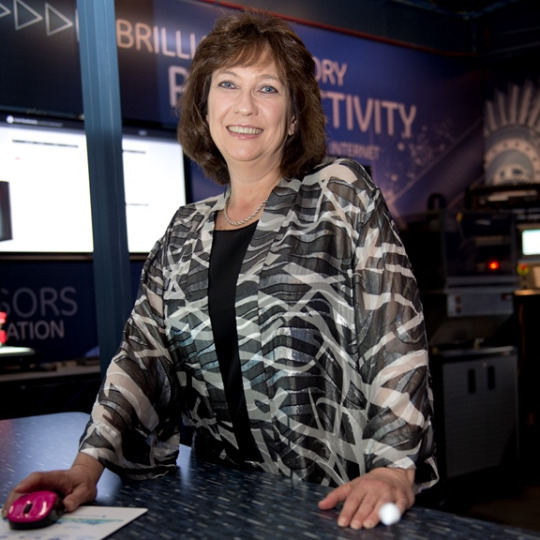
“The speed of change that I see, to me, defines this as a revolution,” says GE’s Christine Furstoss.
The Brilliant Factory also allows teams to work better together. For example, now that parts are designed digitally, designers can share their ideas earlier with manufacturers, get feedback, and 3D print new prototypes sooner.
Furstoss says the biggest challenge her team is facing involves developing common tools — software and IT infrastructure — so designers, manufacturers and field engineers can collaborate in immersive environments over cloud-based computer platforms. She is working with other companies to develop common standards backed by the federally funded Digital Manufacturing and Design Innovation Institute.
Says Furstoss: “We want to move quickly to build something scalable.”