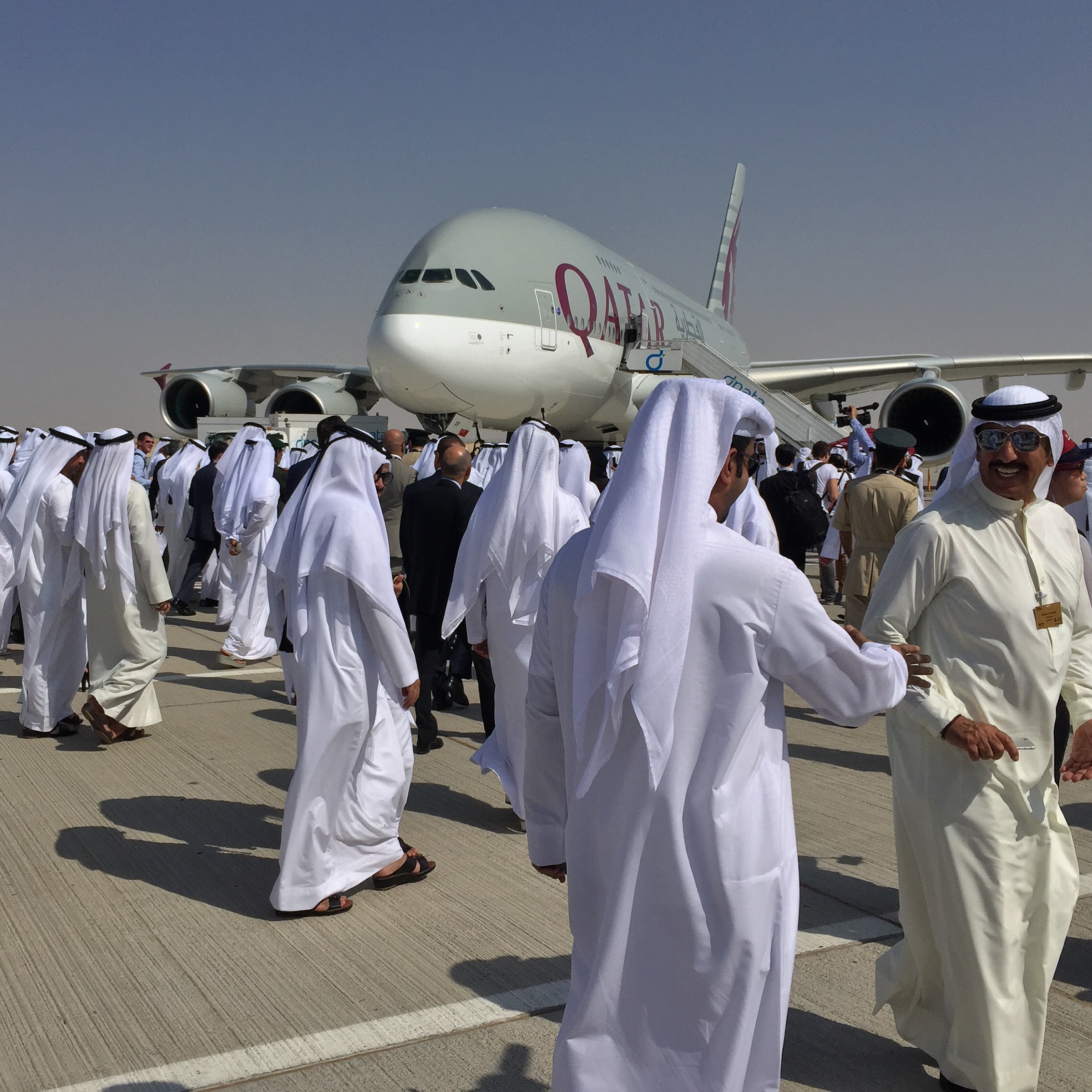
The seaside Tuscan town of Massa defies the Italian stereotype of vineyards and sun-soaked hilltops. True, Michelangelo got stone for David from nearby marble quarries, but today Massa is best known for massive machines and heavy-duty engineering. It’s the birthplace of several industrial goliaths, including GE’s latest jet engine, the GE9X.
GE is developing the engine exclusively for Boeing’s next-generation wide-body plane, the 777X. The GE9X is designed to be the world’s largest jet and most efficient engine with a fan that’s 134 inches in diameter – just under the interior width of a Boeing 737, which clocks in at 139 inches. It will go into service at the end of the decade.
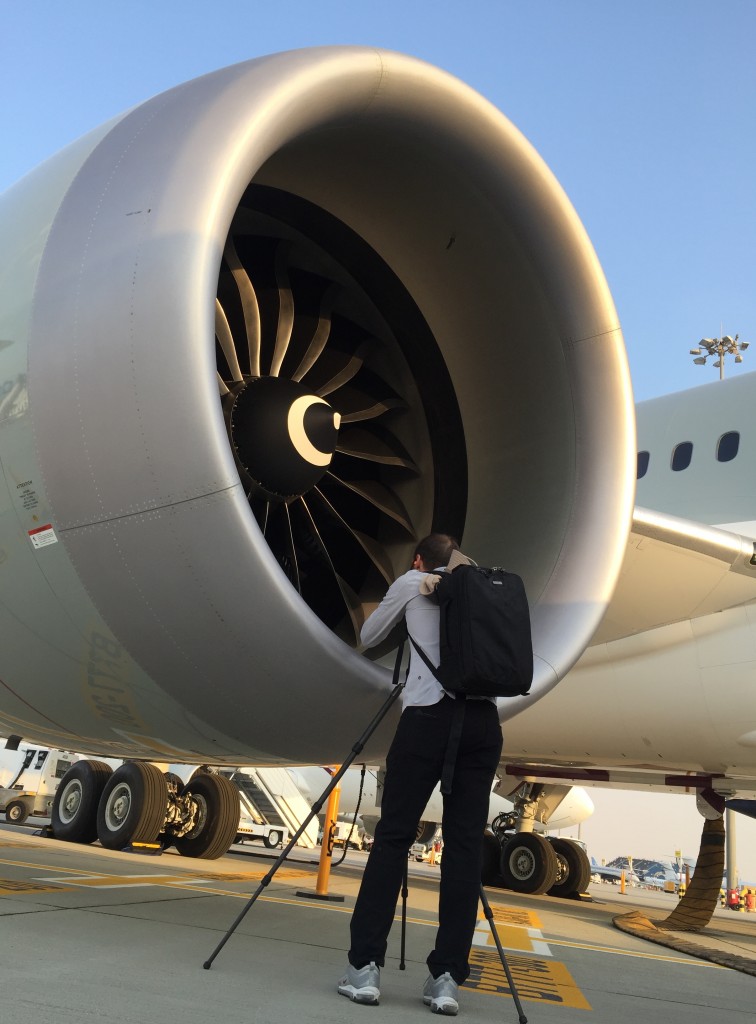
Top: Qatar Airways is one of the Middle Eastern airlines that ordered GE9X engines for its fleet of Boeing 777X planes. Above: The GE9X will the latest high-bypass turbofan engine from GE. This image shows its predecessor, the GEnx, at the 2015 Dubai Air Show. Image credit: GE Reports
GE has already received orders and commitments for 700 GE9x engines valued at $28 billion (list price) from several growing Middle Eastern airlines like Emirates, Qatar and Etihad, as well as Lufthansa, Cathay Pacific and All Nippon Airways. Emirates, Qatar and Etihad, which are present at this year’s Dubai Air Show have ordered 150, 60, and 25 GE9X powered 777X aircraft, respectively. Today, Emirates also signed a $16 billion deal with GE Aviation to service its GE9X engines for a dozen years after they enter service.
What makes the engine special, however, isn’t just its size. It’s also how it is being built. The Massa plant belongs to GE Oil & Gas, and GE Aviation has used it and its engineers to develop a core part of the engine. GE calls this concept of sharing expertise and knowledge the GE Store.
On a typical day, workers at the Massa site test and assemble huge modular power plants that can each generate 116 megawatts for oil and gas installations such as the Gorgon subsea gas field off the coast of Australia. “They have a lot of experience with gas turbines,” says Tim Taylor, a senior engineer for mechanical design at GE Aviation, who was involved in the project. “Since each oil and gas project is pretty much unique, they have a lot of experience with variability and can build a new test stand very quickly.”
The GE Aviation team first arrived in Massa in 2013. Since Italy doesn’t have the same travel visa requirements as the U.S., they were able to invite GE experts from Poland, Germany, India and elsewhere to join the project.
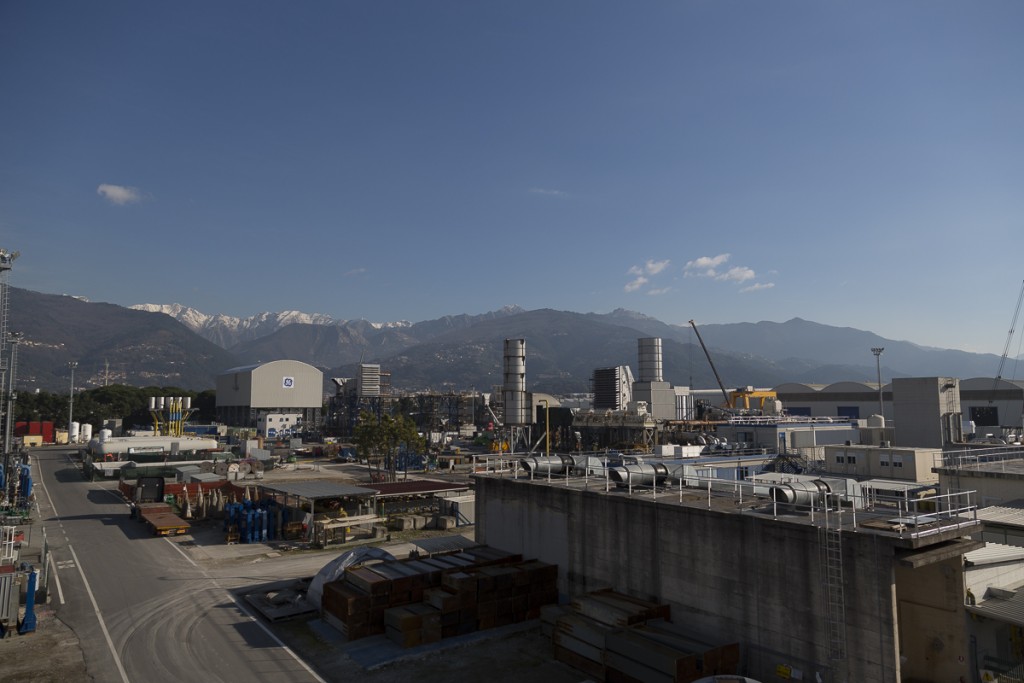
White marble peaks and quarries where Michelangelo got marble for David tower over the Massa plant. Image credit: GE Aviation
The team set up their prototype at one of Massa’s outdoor test stands. “Our test director came from GE Oil & Gas and he set up all the instrumentation and monitoring systems,” Taylor says. “His team designed for us the lubrication and cooling systems so we could move really quickly. It was a bespoke rig.”
The team’s goal was to validate a design for the engine’s high-pressure compressor (HPC) – a key component supplying pressurized air to the combustor of the engine and helps determine its efficiency. “We are using new cobalt-based alloys, new coatings and new aerodynamic designs,” Taylor says. “We had to prove them all.”
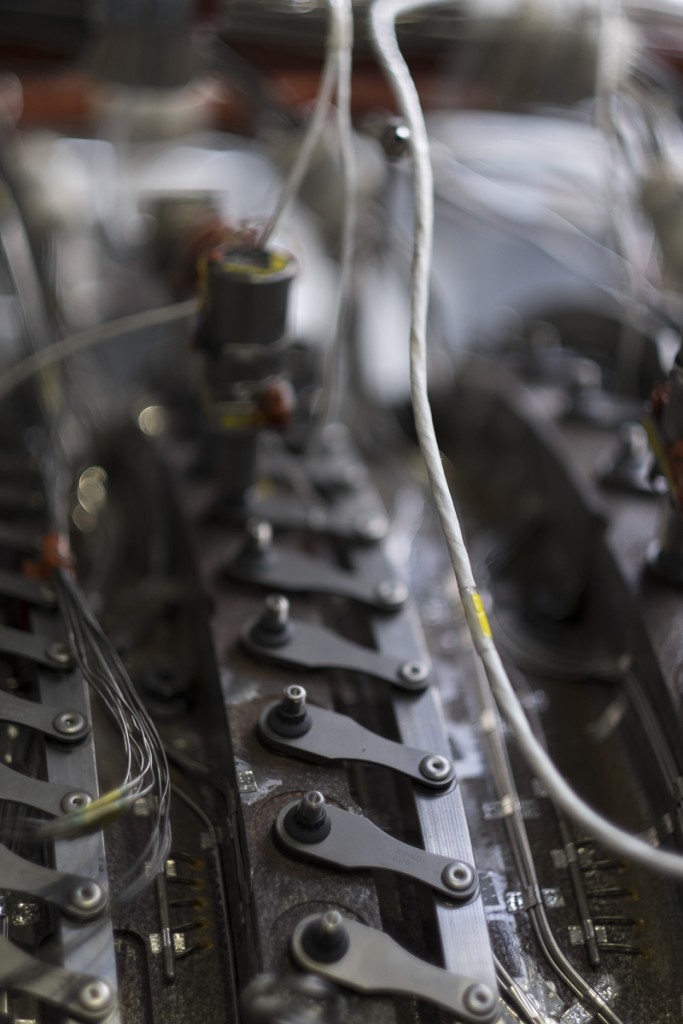
A detailed image of the test turbine showing a ring with variable vanes that help engineers change the pressure inside the engine. Image credit: GE Aviation
The HPC for the GE9X has 11 stages of airfoils designed to compress the air flowing into the combustor chamber 27 times. “Compared to our previous engines, we have more stages and the rotors have a larger radius,” Taylor says. “This means that when we increase the pressure inside the compressor, the temperature also goes up. You don’t get anything for free in nature and we had to make sure that design would hold up to expectations.”
The prototype that the GE Aviation team took to Italy was built at 75-percent scale. The team only needed validation data at 30 percent of the pressure it would see in service, or 300 pounds per square inch, to confirm the design was going in the right direction. “That’s the same amount of pressure you’d feel at 510 feet under the sea, about the limit for World War II submarines,” Taylor says. “You need a tremendous amount of torque to create that pressure. You can’t do this with an electrical motor.”
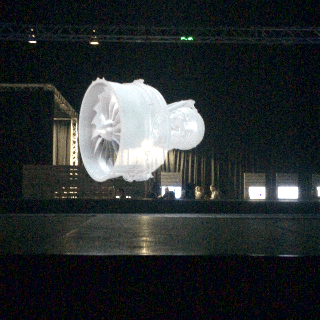
A hologram of the GE9X jet engine at the Minds + Machines conference held last week in Dubai. When the engine enters service at the end of the decade, it will be connected to the Industrial Internet. Image credit: GE Reports
But you can do it with a gas turbine and Taylor and the Oil & Gas team used a model built by their colleagues at GE Power & Water. “It’s funny that this turbine actually uses technology we at GE Aviation had originally developed for our jet engines,” says Taylor. “It kind of completes the circle for the GE Store.”
With the test rig in place, Taylor and his team took the HPC for the new jet engine for a spin. They did a lot of harsh things to it, including testing for stall. During normal flow, air moves from an area of high pressure to a low-pressure environment – just like when air escapes from a party balloon. But a compressor moves air in the opposite direction. “It’s against nature and the air doesn’t want to go that way,” Taylor says. “When you push it too hard, the compressor stalls and burps up a fireball that tears up the engine. We had to prove that our design would work within the safe boundaries.”
Taylor and the team ran two series of tests in Massa. After the first one, they decided to open the front part of the compressor and tweak it to improve performance. The second test series, concluded this year, proved they were on the right path. “We got the efficiency we wanted,” Taylor says. “We could run it without stalling.”
The HPC is now back in the U.S. Another team at GE Aviation coupled it with a combustor and will soon begin testing the pair together.
The combustor for the GE9X includes inner and outer liners made from a ceramic matrix composite (CMC) – a light and heat resistant super material whose first application was inside large GE gas turbines. “At GE, you can’t turn a corner without running into a technology built by some other business,” Taylor says. “It’s the magic of the place.”
When finished, the GE9X will deliver a 10 percent improvement in fuel burn, compared to its older brother, the GE90 engine. One variant of that engine, the GE90-115B, holds the title of the most powerful jet engine ever built. In 2002, it generated 127,900 pounds of thrust at a GE’s jet engine test stand in Peebles, Ohio. The thrust of the Redstone rocket that took Alan Shepard to space was just 76,000 pounds.
The GE90 will likely get to keep the record, but the GE9X will me more efficient. Says Taylor: “You can’t stop progress.”