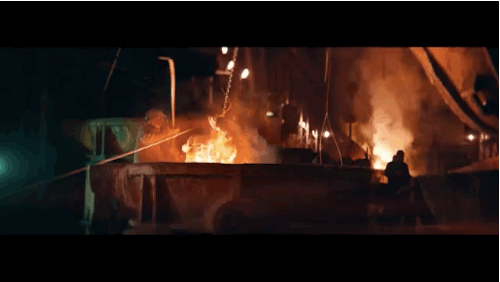
Giving snowballs a chance in the hell of a foundry, catching lightning in a bottle and making a wall talk: Thomas Edison did none of these seemingly impossible things. But then, he never had the opportunity.
This year, GE is celebrating Edison’s birthday, which President Reagan proclaimed as National Inventors Day, by taking on the impossible challenges of lore. On Feb. 11, the company will release videos that prove these feats are “unimpossible.”
Steve Buresh, a materials processing engineer at GE Global Research in Niskayuna, New York, was part of the snowball team. Buresh has spent a decade at GE, working on everything from nuclear reactors to medical imaging machines. He talked to GE Reports about the project.
GE Reports: You task was to send a snowball to hell and bring it back. How did you do it?
Steve Buresh: We pulled together materials scientists, mechanical engineers, physicists and even some chemists. Most of the folks work on jet engines and gas turbines, but others specialize in oil and gas, healthcare and even lighting. In medicine, they are exploring materials for X-ray targets that must take a lot of heat. Their insights were very helpful.
GER: Where did you start?
SB: We pretty quickly agreed that we would build a vessel that could hold the insulation and the snowballs. We focused on a nickel-based super alloy that’s normally used to build gas turbine shrouds and shields and can handle as much as 1,300 degrees Celsius. The wall of the vessel was about an eighth of an inch thick and we lined it with 2 inches of fibrous insulation made from alumina-silicate that’s normally on the outside of things like a jet engine.
GER: That was enough to keep the snow from melting?
SB: That’s not all. We filled the inside of the vessel with dry ice and a 3D-printed plastic sphere divided in the middle. The sphere would sit in the dry ice and hold the snowball. We ran the calculations and estimated we had enough to lower the temperature from 1,100 degrees Celsius on the outside to minus 100 degrees on the inside.
GER: Did you use ordinary plastic for the sphere?
SB: Yes, ABS plastic, the same stuff you might use in your MakerBot. Its main function was to prevent the snowball from getting crushed. The insulation, which was a bit like a blanket, also helped to keep the snowballs from breaking.
GER: What was the most difficult part?
SB: We really didn’t know how the vessel, which weighed more than 50 pounds, would react with the molten metal and whether it would hold. The foundry was in a remote location and we couldn’t bring the tools with us to measure the temperature of the slag we immersed it in. We designed a cage from a cobalt alloy to support it. The vessel was also lighter than the slag and tended to float. We had to hold it under the molten slag.
GER: What happened when you opened it?
SB: Waiting for the vessel to cool down seemed like forever. We lost some of the dry ice and there was a slag and oxide layer on the outside of the vessel, but the snowball were intact. We were elated. When we work with materials in our labs, we make them fail in a controlled way. It’s a graceful failure. Here we were outside our comfort zone.
GER: What’s your one takeaway from the project?
SB: I was involved in making and testing the vessel and designing insulation scheme. We worked on the project just for a few weeks and it was amazing that we pulled it off. It’s really the power of the GE Store, the idea that we have so many experts of different disciplines and can bring them together to leverage that knowledge and experience. I saw it happen.