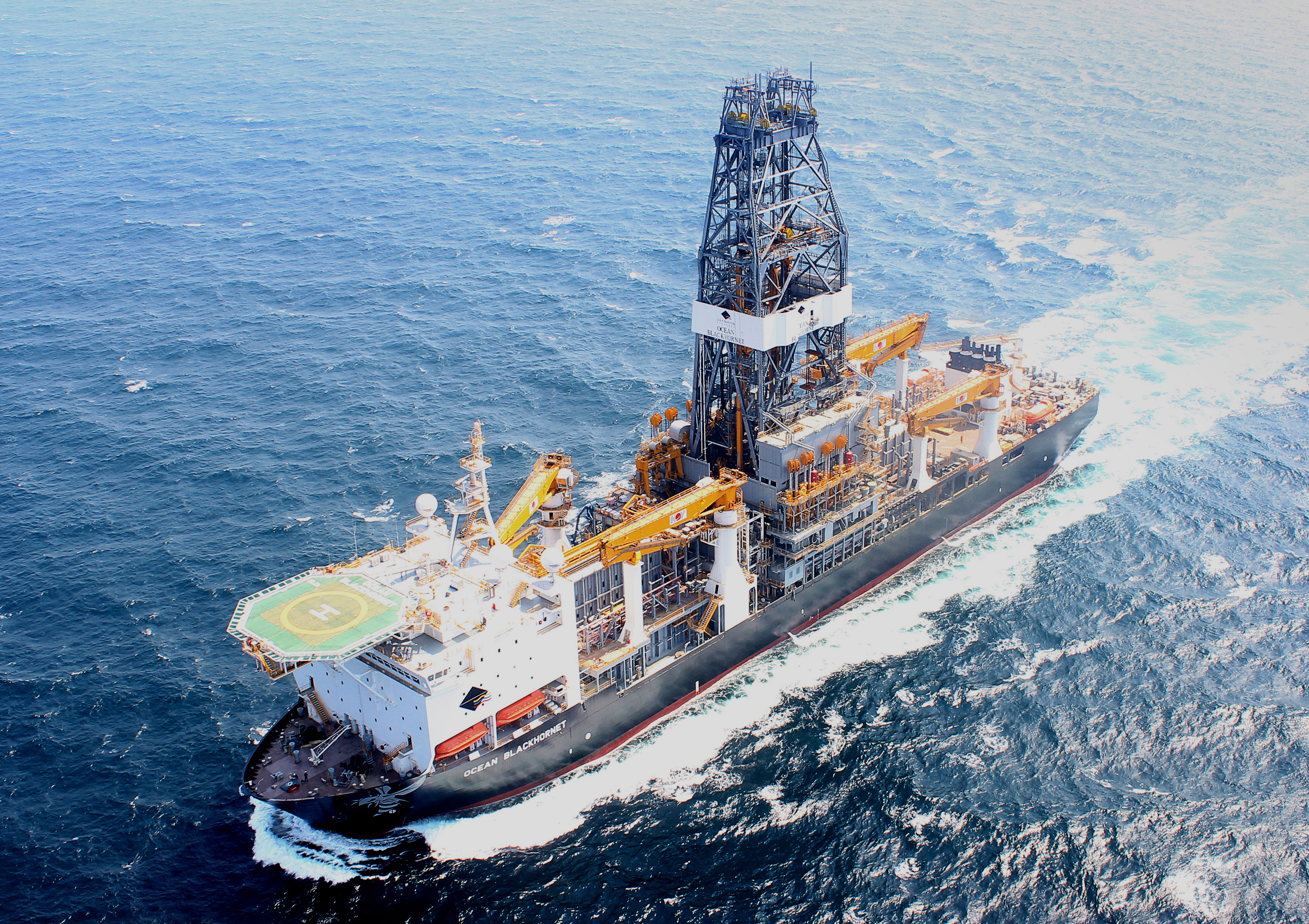
When Marc Edwards joined Diamond Offshore Drilling Inc. as chief executive in 2014, he already knew how dependent offshore drilling rigs were on blowout preventers — valve assemblies designed to prevent oil spills. But he was surprised when he found out how costly it was when those blowout preventers were out of service.
Now, thanks to an innovative service model involving Diamond and GE Oil & Gas, oil companies have a way to save millions of dollars from downtime and repairs. The deal, which could become a blueprint for the rest of the industry, focuses on optimizing blowout preventer performance by adding cloud-based analytics running on GE’s Predix digital platfom to heavy-duty subsea engineering.
The solution is an example of how GE is partnering with customers to solve some of the industry’s toughest challenges by expanding its services offerings, which account for roughly three quarters of the company’s profits.
Blowout preventers (BOPs) are crucial to well construction and ensuring oil drilling doesn’t damage the environment. The stacks of valves, pipes and seals weigh 750,000 pounds and tower 60 feet above seafloor oil wells in order to stop the flow of oil if a company loses control of a well. But they can cause headaches.
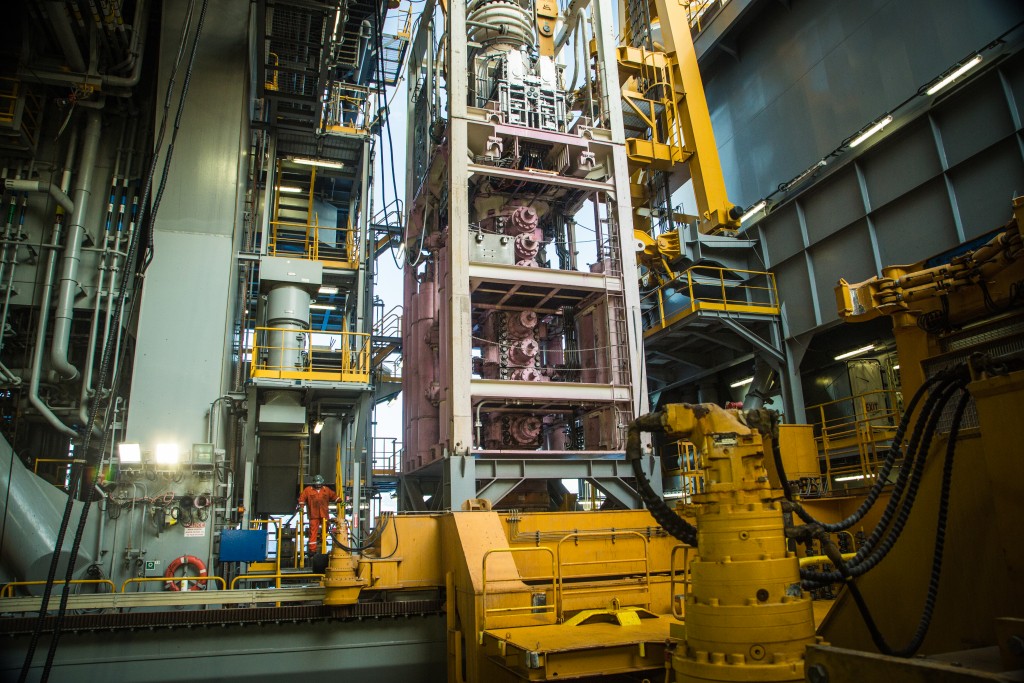
Top Image: Diamond’s drill ship the Hornet carries subsea machines including blowout preventers (the white stack above). Images credit: Diamond Offshore Drilling
When a valve fails, energy companies hoist BOPs from as far down as miles to the surface to find the problem and fix it. Repairs can take several weeks, costing an oil company more than $1 million per day in lost productivity. That way of doing business, Edwards says, is “simply not in the best interest of the stakeholders.”
Edwards previously worked in the hydraulic fracturing industry, which took off because it was able to find a profitable way to get oil and gas out of shale rock. He thought that he could apply the lessons learned in the subsea business, especially in the age of cheap oil. “It was unacceptable,” he says. “There is no other industry that would accept the type of performance reliability that we see in subsea stacks, which costs a lot of money for our clients. There’s significant unproductive time of the drill rig over the well.”
Edwards says a typical deep-sea drilling rig is unproductive about 10-12 percent of the time — and most of that downtime is caused by BOP problems. That can mean more than $35 million of unproductive time annually for just one deep-sea well.
Traditionally, Edwards says, the BOP manufacturer sells the valve that controls the oil flow with a list of spare parts and no maintenance agreement. Imagine if you bought a pickup truck and the manufacturer expected you to source the spare parts and fix the truck yourself. Why, Edwards wondered, is that same setup not considered ridiculous for BOPs?
The new partnership between Diamond and GE changes that business model. Under the agreement, Diamond Offshore has sold eight GE-manufactured stacks, located on drill ships in the U.S. Gulf of Mexico, back to GE for $210 million in a 10-year contract. Now GE owns the assets and is responsible for BOP maintenance. Diamond pays GE for days when the BOP is working. On days when the BOP is not working, Diamond doesn’t pay.
That setup gives GE an incentive to keep the BOP working as often as possible through reliability-driven maintenance. The deal makes sense for the company as it opens the door to using GE software and cloud analytics to predict and prevent downtime and make smarter repairs. GE calls the offering engageDrilling Services. “My clients are applauding this deal,” Edwards says. “They believe it will be material in driving nonproductive time out of deepwater drilling.”
Lorenzo Simonelli, GE Oil & Gas president and chief executive, says engageDrilling Services is a solution that “improves drilling efficiency now and in the future.” The deal reduces risk for the driller and gives GE a steady revenue stream. “We are changing the game by building a new blowout preventer service model for the industry. With improved control, maintenance and servicing of our equipment, we are putting skin in the game and guaranteeing performance,” he says.
Simonelli’s business is already testing other digital systems. Engineers often replace as much as a fifth of BOP parts — including those that are still working fine — every time the machines come to the surface to eliminate potential problems. They effectively rebuild the BOP every five years. But the unneeded work can be minimized thanks to another digital predictive maintenance system called SeaLytics BOP Advisor. It collects and analyzes data about pressures, valves and flows from underwater sensors attached to the machines to determine what needs to be fixed and when.
With oil prices in their deepest downturn since the 1990s, making BOPs more efficient and drilling more productive is something that should make everyone more successful.