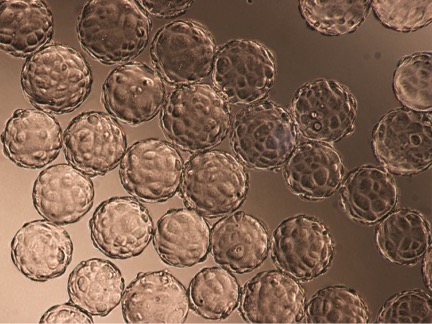
Sugar from plants may not be the first thing that springs to mind when you start thinking about the latest and most promising drugs. But without a special kind of sugar, a new class of revolutionary medicines called biologics targeting everything from diabetes and cancer to immune disorders, such as arthritis, would be extremely hard to make.
Unlike Aspirin or Tylenol, biologics – they are also sometimes called biopharmaceuticals – are the product of live organisms. They are made by genetically modified bacteria or special cell cultures grown in tanks called bioreactors. “The bacteria and cell cultures are really the drug factories,” says Lotta Ljungqvist, head of R&D for bioprocess at GE Healthcare Life Sciences in Uppsala, Sweden. “Protein production is a natural capability of these organisms that can be used to make very powerful drugs. But the drugs have to be extremely pure to avoid unwanted side effects.”
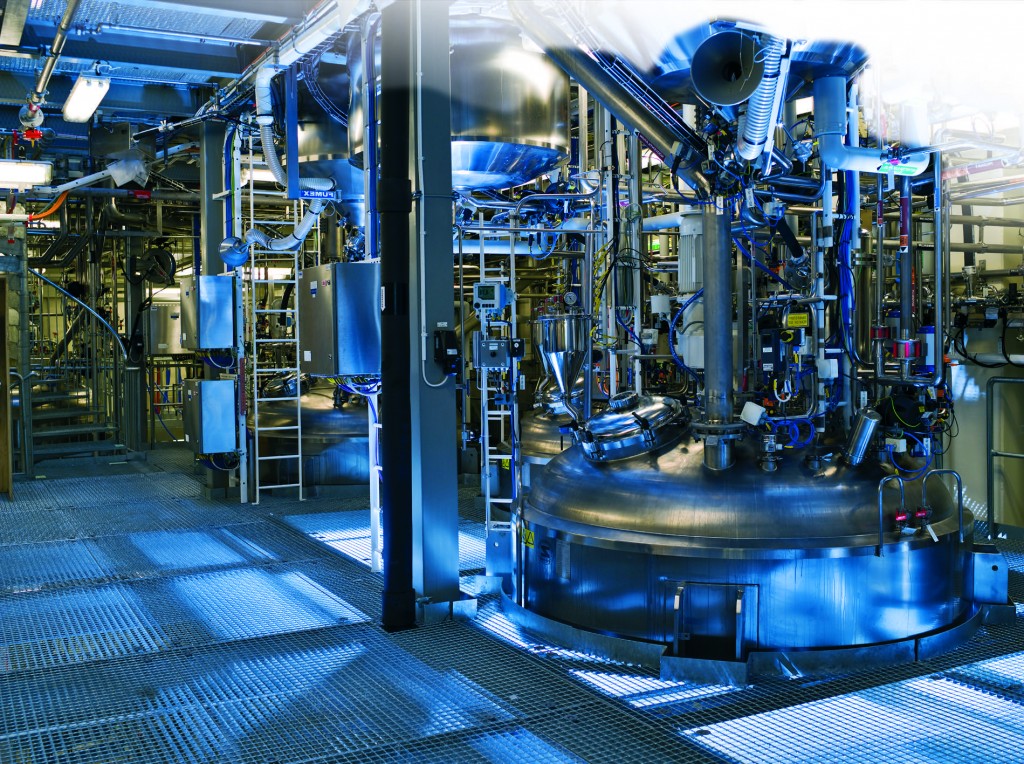
Above: GE’s facility in Uppsala is one of the world’s biggest production facilities for manufacturing of chromatography media. Top Image: Pharma companies use cell cultures for production of biopharmaceuticals and vaccines. In this picture, cells from an African green monkey have attached to small beads. Image credits: GE Healthcare Life Sciences
Scientists tweak the DNA of the bacteria and cells to make molecules like insulin, monoclonal antibodies and even vaccines. Once inside a patient, proteins such as monoclonal antibodies can, for example, attach themselves to cancer cells and mark them like a target. This allows the body’s immune system to see the marked cells and kill them. “We can use biologics to attack new diseases and they don’t have as many side effects as some of the old medicines may have,” Ljungqvist says. “But the cell and microorganism factories produce all kinds of things. We need very sophisticated tools to pick the right proteins from the soup to make sure that the drugs work the way they should.”
The Uppsala factory, which GE acquired with Amersham in 2004, has been developing chromatography resins for decades and several Nobel laureates are connected to the technology.
Pharmaceutical companies grow the “production organisms” – often a strain of E. coli bacteria or special ovary cells from Chinese hamsters – in bioreactors kept at cozy 37 degrees Celsius (98.6 Fahrenheit). They also feed them a steady diet of nutrients. “Just like humans, they need to eat, drink, breath and get rid of waste,” Ljungqvist says.
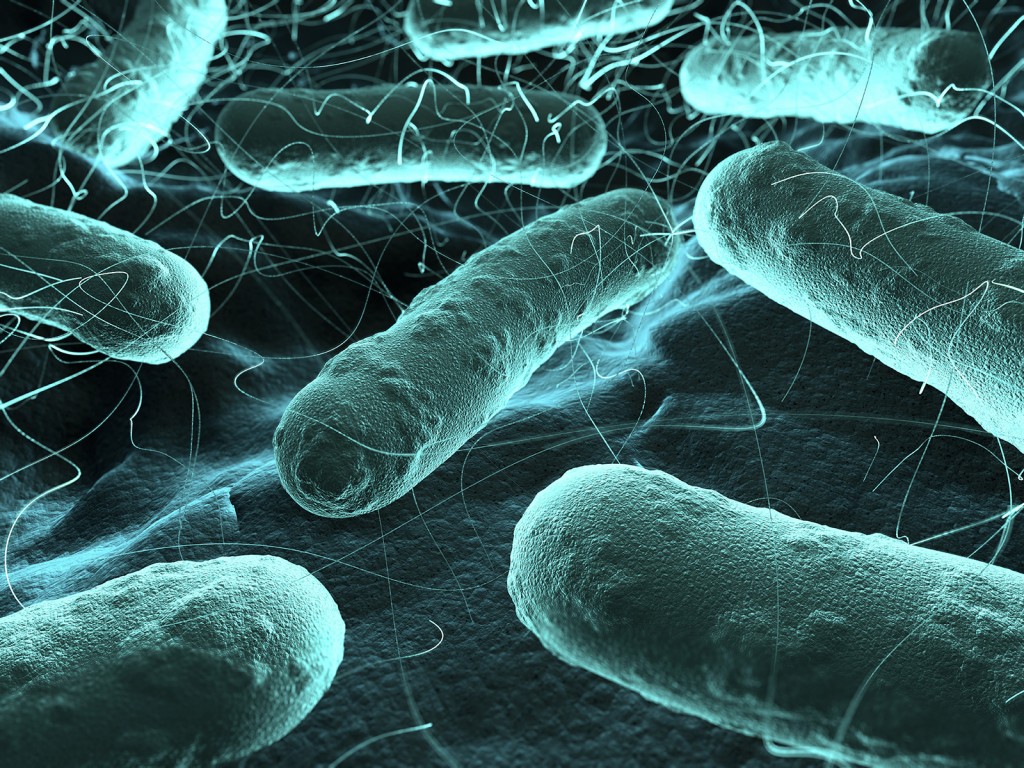
Scientists alter the DNA of bacteria like E.coli to produce proteins for biologics. Image credit: Getty
When the cultures have been growing in the bioreactor tank for a defined time – this can last from one day to several weeks – workers will load the resulting soup which contains a mix of product and contaminants onto a special cylinder, or column, filled with the chromatography resin. Some of these cylinders weigh as much as 11 tons and can purify hundreds of kilos of protein at a time. The resins then stick to the right proteins by exploiting differences in electric charge, size and affinity to water and oil. The rest pass through. Ljungqvist says that GE engineers have perfected some 300 protein-fishing particle combinations to date.
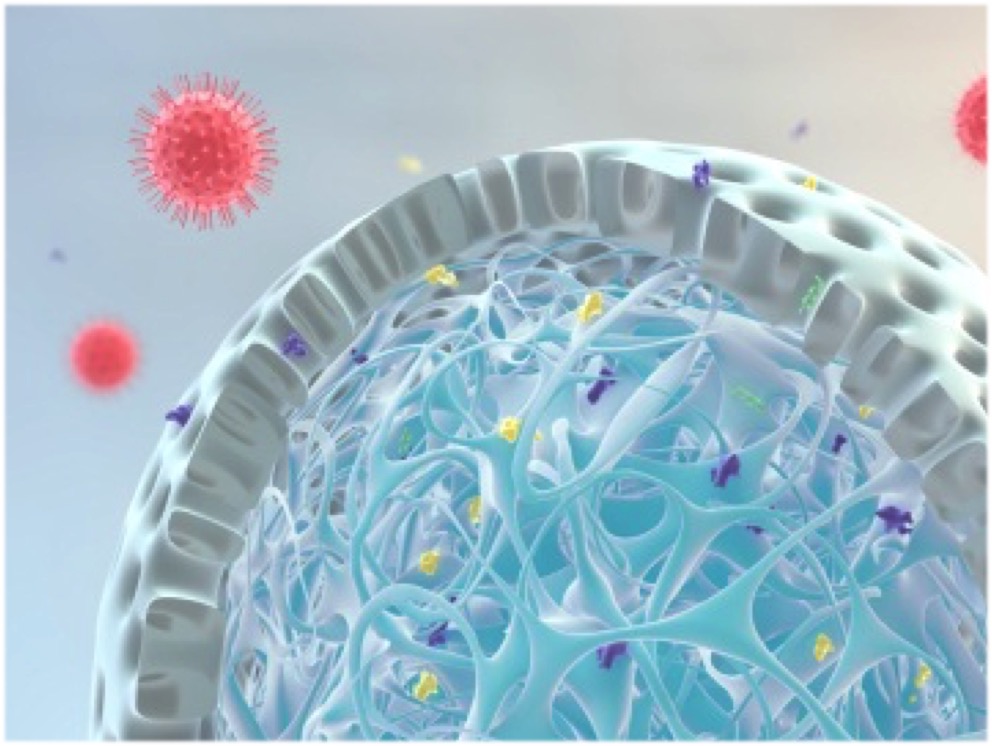
A porous resin particle used to purify vaccines. See proteins pictured in yellow, green and blue captured inside. Image Credit: GE Healthcare Life Sciences
Nigel Darby, head of GE’s bioprocess business, says that biopharmaceuticals is a “healthy segment” estimated to grow with approximately 8 percent per year until 2020. Regulators have approved some 200 biologics, including blockbusters such as Herceptin, Remicade, Humira and Avastin. “Seven of the top 10 drugs now come from the group, where a decade ago there was just one bestseller,” Darby says.
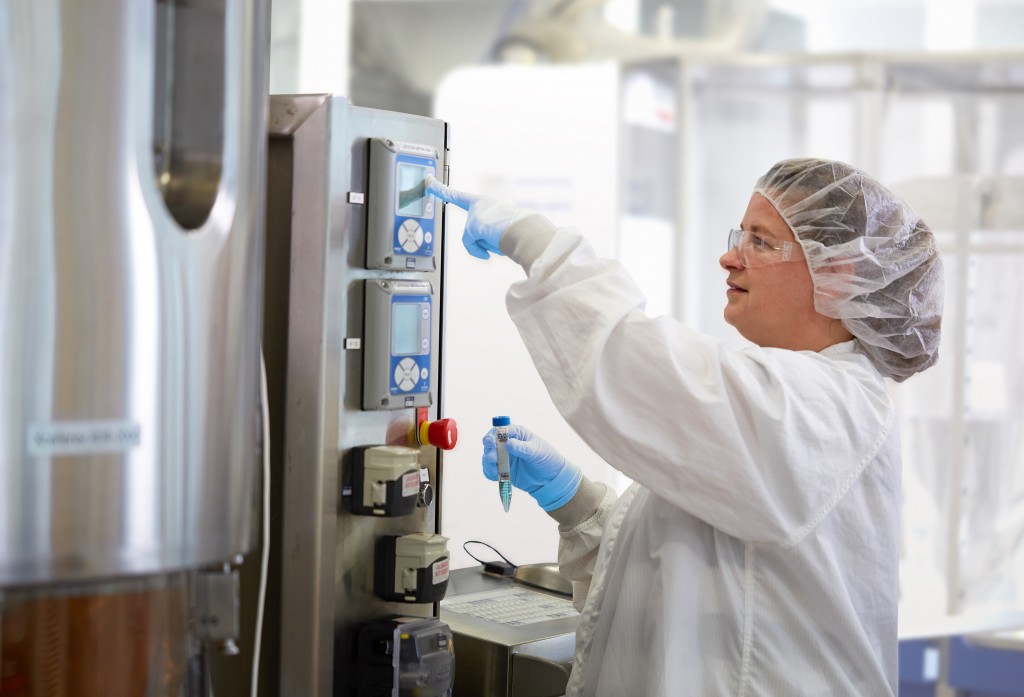
A bioreactor tank used in the production of biopharmaceuticals. Image credit GE Healthcare Life Sciences.
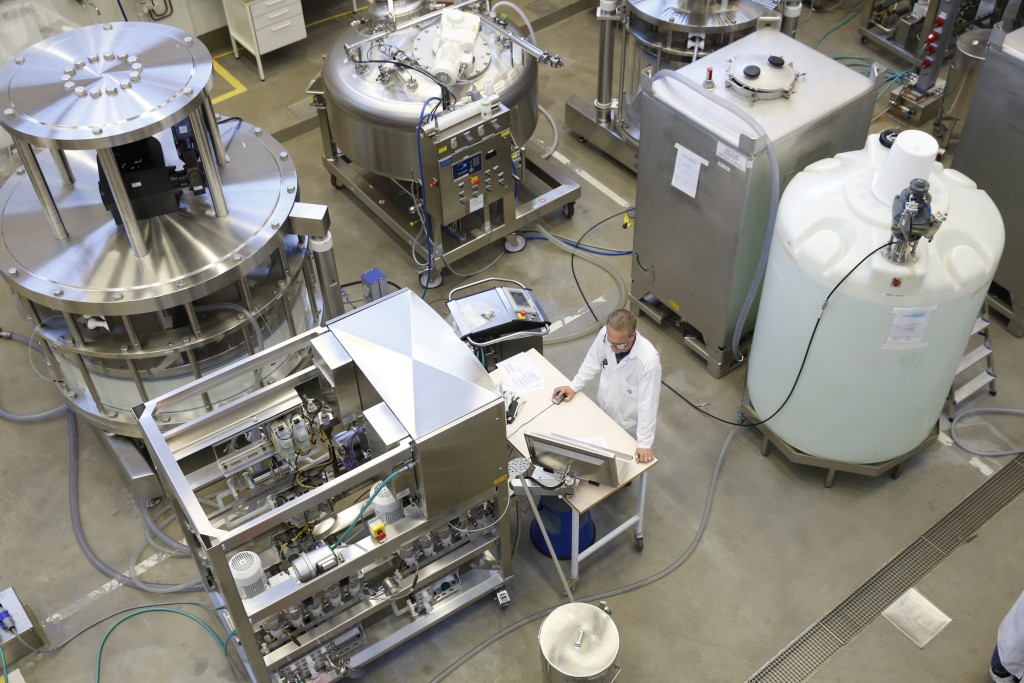
When the production phase is over, the resulting soup with product and contaminants is removed from the bioreactor and loaded onto a special cylinder, or column (see above in upper left corner) for purification. Some columns weigh as much as 11 tons. Image credit GE Healthcare Life Sciences.
Darby says that GE’s business is growing with the market. For example, most of the worlds synthetic insulin is purified on GE resins.
The company is now planning to use software and GE’s Predix cloud platform to gather and analyze data from the biomanufacturing processes to optimize production and increase productivity. The technology continues to evolve to make manufacturing ever more efficient, particularly when making small batches of personalized medicines. “That’s the future of medicine,” Darby says. “You can make medicine that targets just one individual or a very small patient group. It’s very different from medicines for the masses. This is a huge opportunity for a business like ours, but it requires significant changes in the approach to manufacturing.”